Why plastic extrusion is ideal for mass production
Why plastic extrusion is ideal for mass production
Blog Article
Recognizing the Basics and Applications of Plastic Extrusion in Modern Production
In the realm of modern-day manufacturing, the method of plastic extrusion plays an important duty. Unwinding the fundamentals of this process reveals the true convenience and possibility of plastic extrusion.
The Principles of Plastic Extrusion Process
While it may appear complex, the principles of the plastic extrusion procedure are based upon reasonably uncomplicated concepts. It is a production procedure wherein plastic is thawed and then shaped into a constant account with a die. The raw plastic product, typically in the type of pellets, is fed into an extruder. Inside the extruder, the plastic goes through warm and pressure, causing it to melt. The liquified plastic is after that required via a designed opening, called a die, to create a long, continual item. The extruded product is cooled down and afterwards cut to the preferred length. The plastic extrusion process is extensively used in various sectors due to its cost-effectiveness, efficiency, and convenience.
Various Sorts Of Plastic Extrusion Strategies
Building upon the fundamental understanding of the plastic extrusion procedure, it is essential to explore the different strategies associated with this manufacturing approach. Both main strategies are profile extrusion and sheet extrusion. In profile extrusion, plastic is melted and developed right into a constant account, typically made use of to create pipes, poles, rails, and home window frames. On the other hand, sheet extrusion produces big, flat sheets of plastic, which are normally more refined into items such as food packaging, shower curtains, and cars and truck components. Each strategy calls for specialized machinery and specific control over temperature level and pressure to ensure the plastic keeps its form during cooling. Comprehending these techniques is essential to making use of plastic extrusion efficiently in modern manufacturing.

The Function of Plastic Extrusion in the Automotive Sector
A frustrating bulk of parts in modern-day vehicles are products of the plastic extrusion procedure. This process has transformed the vehicle market, transforming it right into a much more efficient, cost-efficient, and versatile production market. Plastic extrusion is primarily made use of in the production of numerous automobile components such as bumpers, grills, door panels, and control panel trim. The procedure offers an attire, constant result, allowing manufacturers to create high-volume get rid of wonderful precision and marginal waste. The lightness of the extruded plastic parts adds to the overall reduction in vehicle weight, enhancing gas effectiveness. Moreover, the toughness and resistance of these components to heat, cold, and influence enhance the durability of vehicles. Therefore, plastic extrusion plays a pivotal function in automobile production.
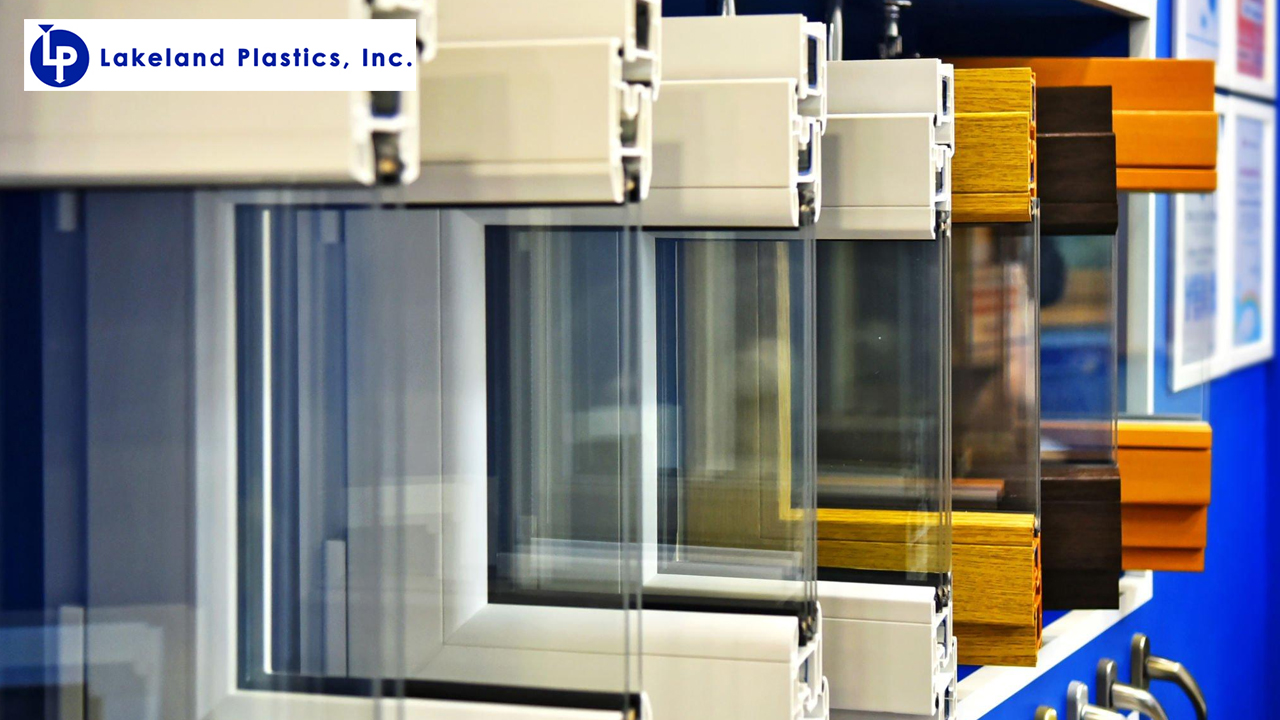
Applications of Plastic Extrusion in Customer Goods Manufacturing
Beyond its significant effect on the vehicle market, plastic extrusion shows similarly reliable try this website in the world of consumer goods manufacturing. This process is critical in producing a large variety of products, from food packaging to household appliances, toys, and also clinical devices. The flexibility of plastic extrusion enables makers to develop and produce complex sizes and shapes with high precision and efficiency. Due to the recyclability of many plastics, squeezed out parts can be recycled, minimizing waste and expense (plastic extrusion). The flexibility, flexibility, and cost-effectiveness of plastic extrusion make it a favored option for many durable goods makers, contributing significantly to the market's development and advancement. The environmental implications of this widespread use call for cautious consideration, a topic to be talked about even more in the succeeding section.
Environmental Effect and Sustainability in Plastic Extrusion
The prevalent use plastic extrusion in manufacturing welcomes scrutiny of its environmental ramifications. As a process that often utilizes non-biodegradable products, the environmental effect can be substantial. Power consumption, waste production, and carbon emissions are all concerns. Market developments are enhancing sustainability. Effective machinery lowers power usage, while waste monitoring systems reuse scrap plastic, lowering basic material demands. In addition, the growth of eco-friendly plastics supplies a more eco-friendly option. Regardless of these renovations, better advancement is required to alleviate the environmental footprint of plastic extrusion. As society leans towards sustainability, producers must adjust to remain viable, stressing the relevance of continuous research and development in this area. this website
Final thought
Finally, plastic extrusion plays an important role in contemporary production, specifically in the auto and durable goods industries. Its adaptability enables the production of a large range of parts with high precision. Its potential for recycling and growth of biodegradable materials supplies a promising method towards lasting practices, thus attending to environmental problems. Understanding the basics important source of this process is crucial to maximizing its applications and benefits.
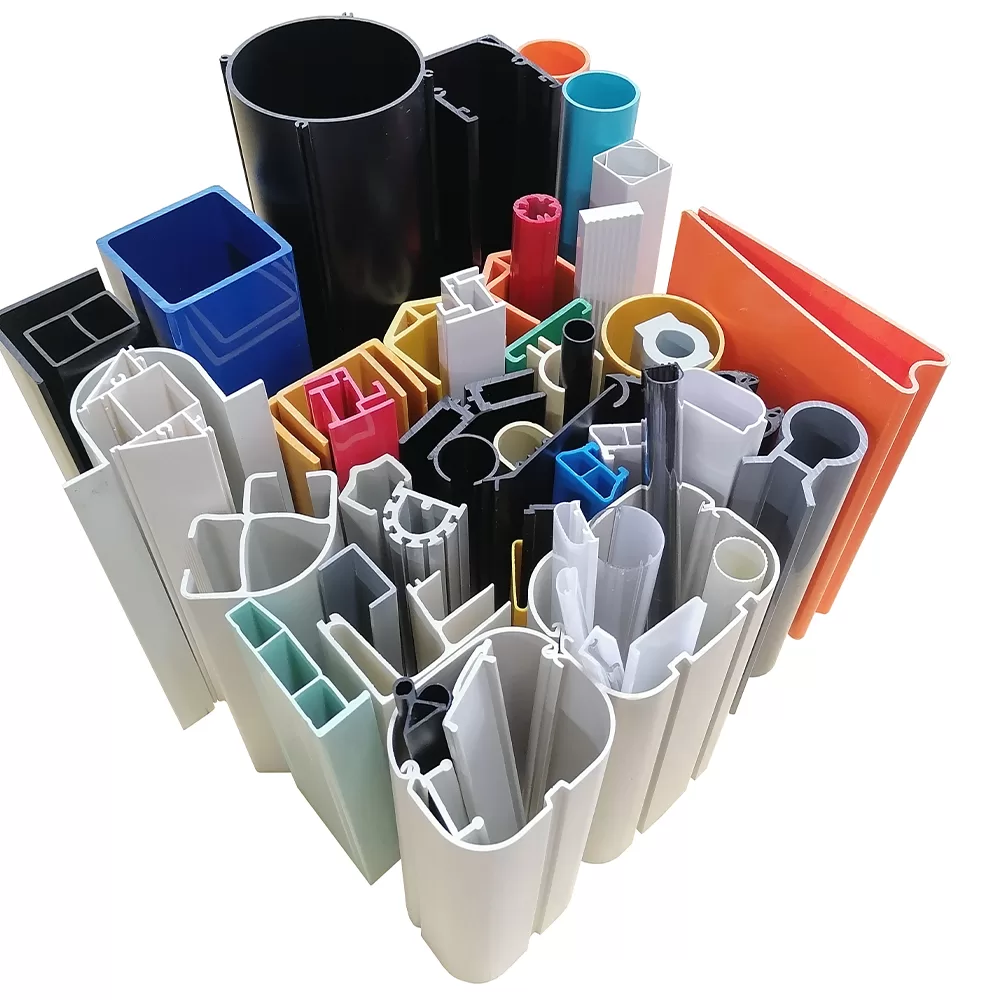
The plastic extrusion process is extensively made use of in different markets due to its cost-effectiveness, effectiveness, and flexibility.
Structure upon the basic understanding of the plastic extrusion procedure, it is necessary to explore the numerous methods included in this manufacturing technique. plastic extrusion. In contrast, sheet extrusion develops huge, level sheets of plastic, which are normally additional processed right into products such as food packaging, shower curtains, and auto components.An overwhelming bulk of parts in modern automobiles are products of the plastic extrusion process
Report this page